Condensing boilers
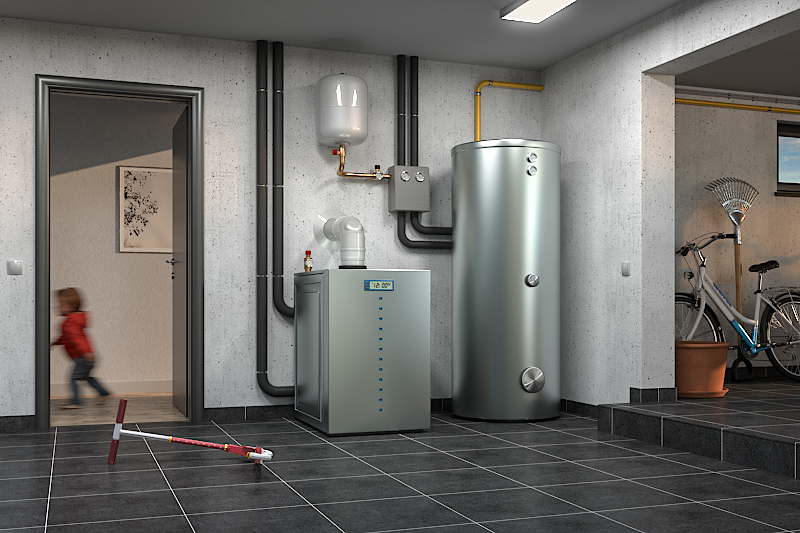
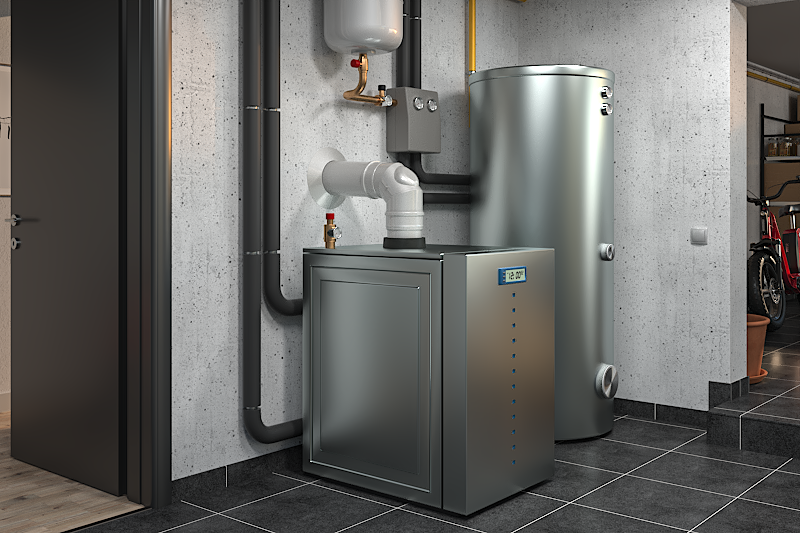
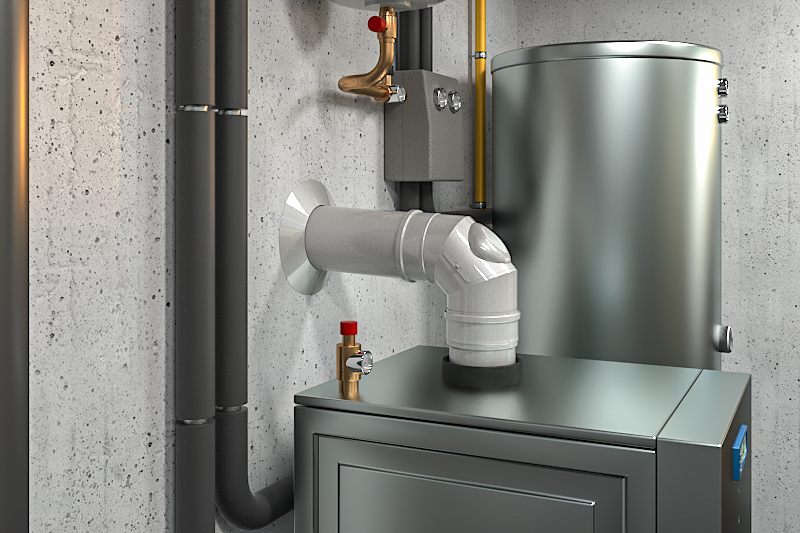
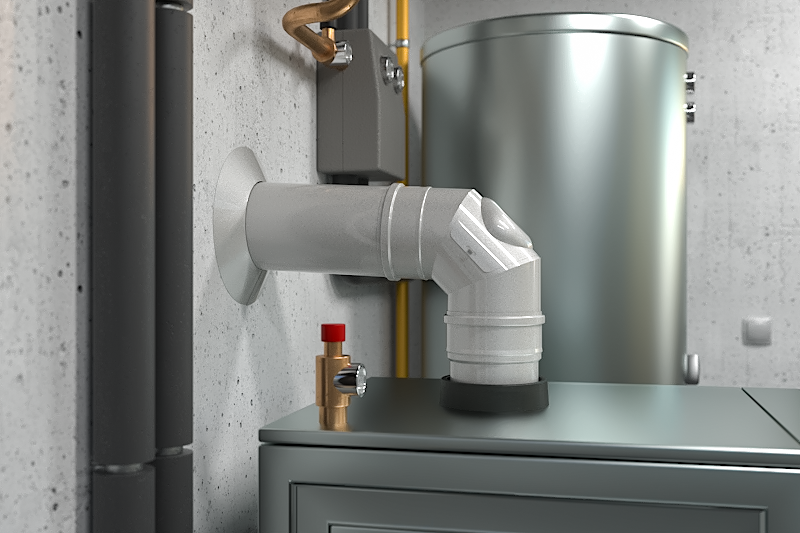
Energy efficient and environmentally friendly
Condensing technology is one of the most efficient, environmentally friendly and technically mature heating systems in the field of fireplaces. A downstream heat exchanger cools the hot exhaust gases until the water vapor they contain condenses. The thermal energy stored in the steam is not lost unused, but can still be actively used.
As a result of this cooling, the flue gases are released to the outside comparatively cool and are then in a range of approx. 104°F to 122°F. Depending on the heating system used and the current mode of operation, this temperature can e.g. B. be higher for drinking water heating.
In contrast to conventional boilers, up to 10% energy and thus heating costs can be saved. These energy savings can be significantly increased if further renovation measures are carried out on a building, such as B. the replacement of old windows or the attachment of a full thermal insulation.
Depending on the pH value and the fuel used, the resulting condensate can still be neutralized and then discharged into the sewage system.
Function of the condensing boiler
The combustion of a fuel produces thermal energy, which is made usable in boilers by heat exchangers and is available as hot heating flow.
In conventional heating boilers, this conversion takes place directly in the boiler, since the flue gas routing inside the boiler is designed in such a way that a large part of the energy contained in the hot flue gases is transferred to a heat carrier, e.g. B. water is released and can thus be used.
However, such fireplaces are not designed to be operated with low exhaust gas temperatures, which is why they usually range in excess of 248°F and the exhaust gases are extracted by the naturally occurring negative pressure.
The residual heat still contained and stored in the combustion gases, in the form of hot steam, cannot be extracted any further in such systems and is therefore released unused into the environment.
For this reason, a heat exchanger can be installed downstream in conventional boilers.
Advantages of condensing technology
Thanks to an integrated heat exchanger, the thermal energy stored in the hot exhaust gases can be better utilized. This significantly increases the efficiency of a condensing fireplace compared to a conventional calorific fireplace. This not only brings energy savings but also lower heating costs, especially if further renovation measures are carried out in connection with the modernization of the heating system.
In the case of condensing boilers, the natural discharge of the flue gases, as is the case with conventional boilers, can no longer take place without problems, since the necessary temperature difference to the outside air is no longer large enough.
For this reason, such systems have a fan inside, which discharges the resulting flue gases to the outside via the exhaust system at a pressure of up to 0.03 psi. The flue gas system or the chimney must be designed in such a way that it is suitable for the resulting overpressure. This is the case if they are marked with pressure class "P1".
It is also important that a moisture-resistant and sufficiently corrosion-resistant system is used, since the condensate can contain components that can attack base or unsuitable materials. If a condensing fireplace for solid fuel e.g. wood pellets are used, for example, care must be taken to ensure that the components used in the flue gas system are pressure-tight and also soot fire-resistant.